該儲罐共設置兩臺液位計:1 臺為伺服液位計、1 臺為雷達液位計、1 臺外貼式超聲波液位開關、1 臺熱電阻、1臺壓力變送器、1 臺壓力表。
2、臺液位計中伺服液位計選用高精度計量及用來做儲罐計量,雷達液位計為控制及用于與高液位開關做聯鎖,關閉罐根閥。
從PID 圖中可以看出從PID 圖中可以看出雖然增加了SIS 系統,但是接入其中的信號并不多,只有一點AI、一點DI、一點DO。其余信號仍然在DCS 系統中進行檢測及報警。
設計的SIS 系統具體聯鎖控制如下:當儲罐的液位計或液位開關任一液位高于設定值時,SIS 系統進行聯鎖,關閉儲罐罐根切斷閥,防止儲罐罐液位繼續(xù)升高,引發(fā)冒罐危險[1] 。
4、SIS 系統設計
4.1 SIS 系統的設置原則
罐區(qū)SIS 系統,作為全廠SIS 系統的組成部分,根據裝置的特點,實現罐區(qū)內重要的安全聯鎖保護、緊急停車系統及關鍵設備聯鎖保護。SIS 系統設置在現場機柜室,設置獨立的控制器,以確保人員及生產裝置、重要機組和關鍵設備的安全。SIS 系統的安全綜合等級根據相應的要求進行考慮。SIS 系統按照DIN V VDE0801 和DIN V 19250 標準,采用TüV 或AK6 安全認證的SIL3 級的安全可編程序控制器(Programmable Logic Controller - PLC) 完成裝置的緊急停車(EmergencyShut-Down - ESD) 和緊急泄壓(EmergencyDepression - EDP)。SIS 系統按照故障安全型設計,與DCS系統實時數據通訊。SIS 系統設工程師站,SOE 站,相應的報警及操作通過輔助操作臺上開關、按鈕、聲光報警裝置和DCS 系統的操作站來完成。罐區(qū)SIS 系統具有報警事件順序記錄功能(SOE),在中央控制室和現場機柜室各設置一套工程師站,用于SIS 系統的組態(tài)、下裝、調試和日常維護以及報警事件順序的記錄。中央邏輯控制器、輸入/ 輸出卡件、SIS 系統內部的安全網絡、供電單元、與DCS 系統通信的單元均采用冗余結構。SIS 系統應配有HART 信息采集器,用于采集現場智能儀表HART 信息,并通訊至AMS 系統。SIS 與DCS 通信卡必須是冗余配置, 且冗余的兩個通信接口不應在同一塊通信卡上。冗余數據通信系統應能夠自動切換,并可進行系統診斷報警。在切換時不允許有數據丟失。通信系統為控制站與控制站之間、控制器與工程師站/SOE 工作站提供可靠的高速數據傳輸。傳輸速率不小于100Mbps。SIS 系統支持標準通信協議,冗余容錯串行通信方式。SIS 與DCS 通信協議為MODBUS RTU 或TCP/IP。DCS 系統為主站,SIS 系統為從站。所有部件都應抗每米10 毫伏場強的電磁及無線電干擾。SIS 系統具有時鐘同步的性能, SIS 系統控制器的時鐘在系統上電和更換時鐘卡件后,能夠自動進行同步。SIS 系統時鐘同步信號來自于DCS 系統。
根據《石油化工儀表系統防雷工程設計規(guī)范》進行儀表系統防雷工程設計。SIL3 回路的現場儀表側及控制室(現場機柜室)側配置防雷電浪涌保護器。
在工廠調試完成后,有20% 已經接好線的輸入/ 輸出(I/O) 點作為備用;在端子接線柜中,有20% 的裕量端子作為備用;在系統機柜中,有20% 的裕量空間用于安裝I/O 卡件。
在工廠調試完成后,處理器、數據存貯器和數據通信網絡的負載最高不超過40%;電源單元的負載最多達到其能力的50%;應用軟件和通信系統有30% 的擴展能力。
4.2 SIS 系統網絡結構
本項目采用冗余、容錯結構的故障安全型SIS 系統,安全等級達到SIL3。
根據圖2 罐區(qū)網絡結構圖,可見:罐區(qū)單元主要硬件設備為:1 臺系統柜、3 臺輔助柜(端子柜、繼電器柜、安全柵柜)、2 臺SOE 工程師站、2 臺交換機、1 臺打印機。
4.3 SIS 系統軟件要求
1) 軟件組態(tài):編程語言應符合IEEC 61131-3 工業(yè)標準。
2) 軟件組態(tài)的安全性:采用PROM 或EPROM 存儲器存儲應用軟件,提供防止未被授權人員修改程序的功能。軟件應能在線修改及下裝。
3) 編程軟件:工程師站用于修改控制程序,診斷顯示,離線/ 在線程序調試和現場裝置的維護。系統軟件包括系統診斷,工程,監(jiān)視和刪除故障功能。
4) 系統應提供重要的時序事件記錄(SOE)和過程歷史報告。
5、結束語
由于石油化工重大危險源本身存在的巨大危害性及其可能造成二次危害的特性,對于石油化工重大危險源的安全控制工作至關重要。對于儲存大量易燃易爆、可燃有毒介質的化工項目,構成重大危險源的儲罐區(qū)采用安全儀表系統(SIS)進行安全監(jiān)控及聯鎖控制系統的設計是符合時代發(fā)展趨勢的。
2、臺液位計中伺服液位計選用高精度計量及用來做儲罐計量,雷達液位計為控制及用于與高液位開關做聯鎖,關閉罐根閥。
從PID 圖中可以看出從PID 圖中可以看出雖然增加了SIS 系統,但是接入其中的信號并不多,只有一點AI、一點DI、一點DO。其余信號仍然在DCS 系統中進行檢測及報警。
設計的SIS 系統具體聯鎖控制如下:當儲罐的液位計或液位開關任一液位高于設定值時,SIS 系統進行聯鎖,關閉儲罐罐根切斷閥,防止儲罐罐液位繼續(xù)升高,引發(fā)冒罐危險[1] 。
4、SIS 系統設計
4.1 SIS 系統的設置原則
罐區(qū)SIS 系統,作為全廠SIS 系統的組成部分,根據裝置的特點,實現罐區(qū)內重要的安全聯鎖保護、緊急停車系統及關鍵設備聯鎖保護。SIS 系統設置在現場機柜室,設置獨立的控制器,以確保人員及生產裝置、重要機組和關鍵設備的安全。SIS 系統的安全綜合等級根據相應的要求進行考慮。SIS 系統按照DIN V VDE0801 和DIN V 19250 標準,采用TüV 或AK6 安全認證的SIL3 級的安全可編程序控制器(Programmable Logic Controller - PLC) 完成裝置的緊急停車(EmergencyShut-Down - ESD) 和緊急泄壓(EmergencyDepression - EDP)。SIS 系統按照故障安全型設計,與DCS系統實時數據通訊。SIS 系統設工程師站,SOE 站,相應的報警及操作通過輔助操作臺上開關、按鈕、聲光報警裝置和DCS 系統的操作站來完成。罐區(qū)SIS 系統具有報警事件順序記錄功能(SOE),在中央控制室和現場機柜室各設置一套工程師站,用于SIS 系統的組態(tài)、下裝、調試和日常維護以及報警事件順序的記錄。中央邏輯控制器、輸入/ 輸出卡件、SIS 系統內部的安全網絡、供電單元、與DCS 系統通信的單元均采用冗余結構。SIS 系統應配有HART 信息采集器,用于采集現場智能儀表HART 信息,并通訊至AMS 系統。SIS 與DCS 通信卡必須是冗余配置, 且冗余的兩個通信接口不應在同一塊通信卡上。冗余數據通信系統應能夠自動切換,并可進行系統診斷報警。在切換時不允許有數據丟失。通信系統為控制站與控制站之間、控制器與工程師站/SOE 工作站提供可靠的高速數據傳輸。傳輸速率不小于100Mbps。SIS 系統支持標準通信協議,冗余容錯串行通信方式。SIS 與DCS 通信協議為MODBUS RTU 或TCP/IP。DCS 系統為主站,SIS 系統為從站。所有部件都應抗每米10 毫伏場強的電磁及無線電干擾。SIS 系統具有時鐘同步的性能, SIS 系統控制器的時鐘在系統上電和更換時鐘卡件后,能夠自動進行同步。SIS 系統時鐘同步信號來自于DCS 系統。
根據《石油化工儀表系統防雷工程設計規(guī)范》進行儀表系統防雷工程設計。SIL3 回路的現場儀表側及控制室(現場機柜室)側配置防雷電浪涌保護器。
在工廠調試完成后,有20% 已經接好線的輸入/ 輸出(I/O) 點作為備用;在端子接線柜中,有20% 的裕量端子作為備用;在系統機柜中,有20% 的裕量空間用于安裝I/O 卡件。
在工廠調試完成后,處理器、數據存貯器和數據通信網絡的負載最高不超過40%;電源單元的負載最多達到其能力的50%;應用軟件和通信系統有30% 的擴展能力。
4.2 SIS 系統網絡結構
本項目采用冗余、容錯結構的故障安全型SIS 系統,安全等級達到SIL3。
根據圖2 罐區(qū)網絡結構圖,可見:罐區(qū)單元主要硬件設備為:1 臺系統柜、3 臺輔助柜(端子柜、繼電器柜、安全柵柜)、2 臺SOE 工程師站、2 臺交換機、1 臺打印機。
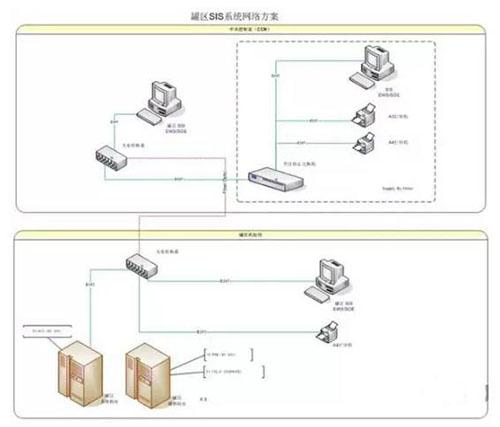
1) 軟件組態(tài):編程語言應符合IEEC 61131-3 工業(yè)標準。
2) 軟件組態(tài)的安全性:采用PROM 或EPROM 存儲器存儲應用軟件,提供防止未被授權人員修改程序的功能。軟件應能在線修改及下裝。
3) 編程軟件:工程師站用于修改控制程序,診斷顯示,離線/ 在線程序調試和現場裝置的維護。系統軟件包括系統診斷,工程,監(jiān)視和刪除故障功能。
4) 系統應提供重要的時序事件記錄(SOE)和過程歷史報告。
5、結束語
由于石油化工重大危險源本身存在的巨大危害性及其可能造成二次危害的特性,對于石油化工重大危險源的安全控制工作至關重要。對于儲存大量易燃易爆、可燃有毒介質的化工項目,構成重大危險源的儲罐區(qū)采用安全儀表系統(SIS)進行安全監(jiān)控及聯鎖控制系統的設計是符合時代發(fā)展趨勢的。